As industries increasingly embrace automation, palletizing has emerged as a critical area for improving efficiency and productivity. Automatic palletizers offer a seamless solution to stacking and organizing products, eliminating the need for time-consuming and labour-intensive manual processes. By enhancing speed, accuracy, and load stability, these machines have revolutionized the end-of-line operations for businesses across various industries. In this blog, we’ll delve into five compelling reasons why investing in an automatic palletizer can elevate your production process, reduce costs, and create a safer, more efficient workplace.
Prioritized Employee Well-Being
One of the most significant advantages of investing in an automatic palletizer is its ability to prioritize employee health and safety by eliminating the physically demanding tasks associated with manual palletizing. Repeated heavy lifting, bending, and stacking can lead to long-term injuries, fatigue, and workplace accidents, all of which negatively impact employee morale and productivity. Automatic palletizers take over these heavy tasks, creating a safer and more ergonomic work environment for your team.
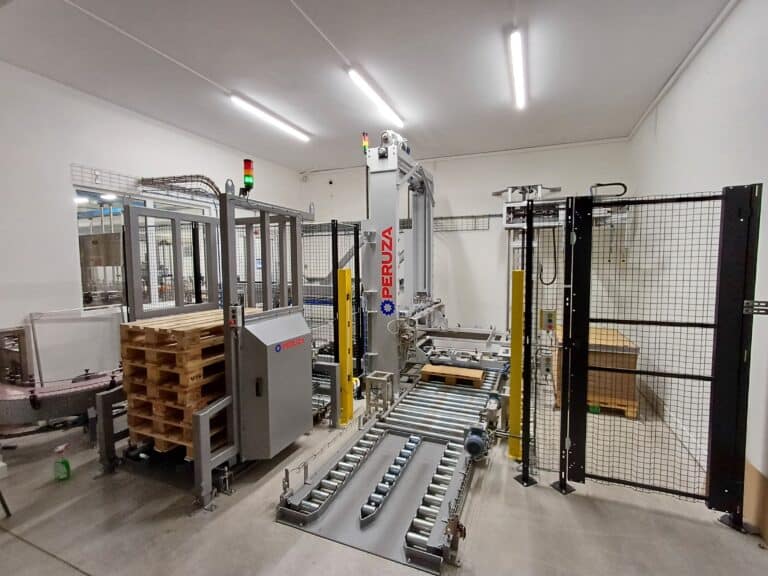
Reduced Labour Costs and Enhanced Efficiency
Automatic palletizers are a game-changer when it comes to reducing labour requirements while maintaining high productivity. By automating the palletizing process, businesses can achieve significant cost savings by reallocating or minimizing the need for manual labour. This reduction in manual intervention not only cuts labour expenses but also minimizes errors, ensures consistent pallet quality, and allows remaining staff to focus on higher-value tasks. With less dependency on manual labour, companies can optimize operations and improve overall production efficiency without compromising output quality.
Integrated Quality Control for Enhanced Accuracy
Automatic palletizing systems can be seamlessly equipped with advanced quality control mechanisms to ensure only the best products are processed and shipped. These systems can quickly detect issues such as broken boxes, improperly sealed cartons, or incomplete packaging before they are palletized. By integrating sensors, vision systems, and automated rejection mechanisms, the palletizer becomes a dual-purpose tool—optimizing both product stacking and quality assurance. This real-time inspection not only prevents defective products from reaching customers but also reduces rework and waste, saving both time and resources. With the added capability of fast quality control, automated lines ensure consistent product standards while maintaining high-speed operation, ultimately boosting customer satisfaction and protecting brand reputation.
Integration with Smart Factory Systems
Automatic palletizers can integrate seamlessly with Industry 4.0 solutions, such as Manufacturing Execution Systems (MES), warehouse management systems (WMS), and Internet of Things (IoT) technology, providing a smarter and more connected production environment. These integrations enable automatic palletizers to communicate with other systems in real time, allowing for continuous data gathering, monitoring, and analysis of production processes. By collecting information on factors such as cycle times, machine performance, and product throughput, businesses gain valuable insights into operational efficiency, equipment utilization, and potential bottlenecks. The ability to analyze this data empowers companies to make data-driven decisions that enhance productivity, reduce downtime, and optimize resource allocation.
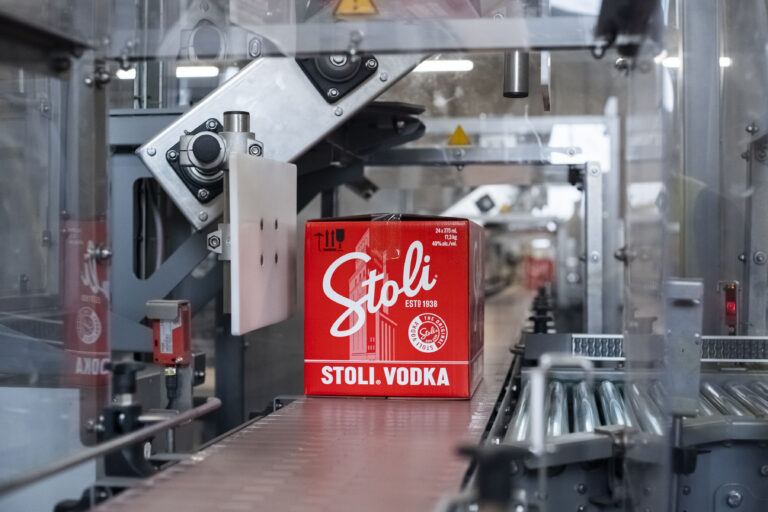
Case Study of High Speed Palletizer
Before | After | |
Workers on a task | 2 workers | 0.5 workers |
Load for one worker | 3 tonnes per hour | 0 tonnes per hour |
In a recent project of ours, a manufacturing facility replaced manual palletizing with an automated solution PERUZA High Speed Palletizer, significantly reducing the physical burden on its workforce. Previously, a single operator was responsible for manually lifting and stacking loads equivalent to three tonnes per hour—a task that led to excessive fatigue and increased risk of injury. With the introduction of an automated palletizer, this heavy workload was entirely eliminated, allowing operators to focus on supervising and managing the process rather than performing labour-intensive tasks. This not only improved workplace safety but also boosted efficiency and employee satisfaction.
The PERUZA High-Speed Palletizer, capable of handling up to 30 boxes per minute and assembling 15 five-layer pallets per hour, further optimized labour requirements. The implementation effectively reduced the need for two full-time operators to just 0.5 operators per shift. Now, during a typical shift, a single operator only needs to dedicate half of their time to tasks such as changing recipes and transferring finished pallets to the wrapping machine.
To Sum Up
In summary, the shift to automated palletizing solutions, such as the PERUZA High Speed Palletizer, demonstrates a transformative impact on industrial operations. By eliminating physically demanding tasks, reducing labour costs, ensuring product quality, and integrating seamlessly with smart factory systems, these innovations significantly enhance productivity and workplace safety. As seen in real-world applications, the adoption of automatic palletizers not only optimizes operational efficiency but also empowers businesses to adapt to the demands of modern manufacturing, fostering a safer, more sustainable, and forward-thinking production environment.