In the world of food processing every step matters. Before products are processed, portioned or packaged, they usually need to go through one crucial stage before: grading. This is the process of sorting products based on physical characteristics such as size or weight to ensure consistency and optimize downstream processes.
Whether you’re working in a fishery handling tons of herring or a poultry plant preparing chicken fillets, automated grading systems can significantly improve both product quality and production speed.
Why Grading Is Important
Grading plays a vital role in maintaining processing efficiency and final product quality, but its importance goes beyond internal operations. Let’s break it down:
- Processing Quality
Uniform products are easier to portion, cook or package. Machines that cut or pack rely on consistent sizes or weights to work correctly. Grading ensures that only suitable products move forward, reducing waste and machine errors.
- Consumer Expectations
In the retail world, presentation matters. When a consumer opens a package of chicken fillets or frozen herring, they expect the contents to be uniform. Uneven product sizes can lead to dissatisfaction, overcooking or undercooking and even lost customer trust. Grading helps deliver a professional, premium look that meets customer expectations.
Manual vs. Automated Grading
While manual grading by hand is still practiced in small operations, it falls short in large-scale environments where speed, precision, and consistency are must. Manual grading is labor-intensive, less accurate and can introduce variability that automated systems eliminate.
Automated graders — whether roller graders or flow graders— offer:
- Improved hygiene and product handling
- Higher throughput with fewer workers
- Better traceability and data collection
Grading Small Fish Like Herring – The Role of Roller Graders
For smaller products like herrings, shrimps or mackerels size-based grading is typically the most effective. Here roller graders come into play.
Roller graders work by letting fish pass over a series of rollers with increasing gaps. As the rollers rotate, fish fall through the gaps that match their width. This is a fast and efficient way to sort products into different size categories for further processing like batching, marinating or packaging.
Key advantages:
- High-speed throughput
- Minimal handling, preserving fish quality
- Suitable for wet and slippery products like herring
Roller graders are widely used in fish processing facilities where consistent size distribution improves portioning and enhances product appearance in the final packaging.
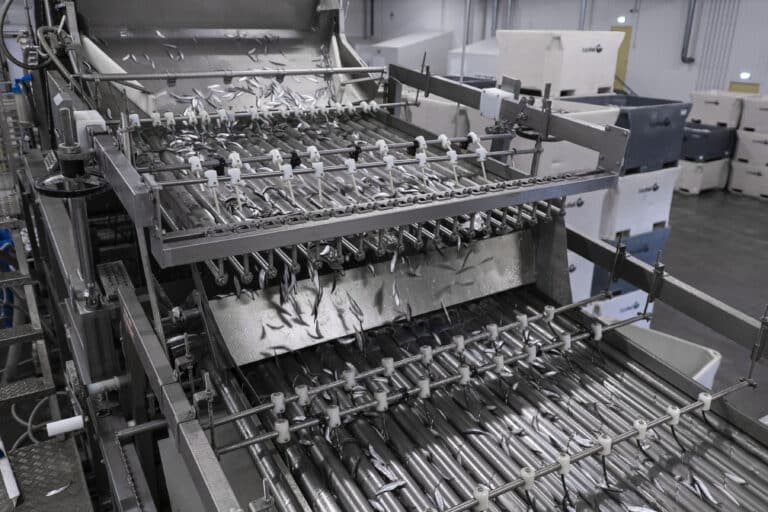
Grading Poultry Fillets by Weight – The Precision of Flow Weight Graders
When processing bigger products, for example poultry fillets, whole fish or cuttlefish, weight becomes the critical factor. Customers expect packs of chicken fillets to have not only uniform size but also precise weight distribution. This is where flow graders excel.
PERUZA Flow Weight Grader is engineered to grade very precisely and fast medium to large products. It dynamically weighs each product as it moves through the system and sorts it into designated weight categories. This enables processors to:
- Create uniform retail packs
- Minimize product giveaway with target batching
- Meet strict portioning requirements for foodservice or export markets
PERUZA Flow Weight Grader can grade up to 120 products per minute. It also features smart software that tracks grading results in real time, helping processors make data-driven decisions.
To Sum Up
Grading is not just a technical step — it’s a strategic advantage in fish and poultry processing. From roller graders for herring, shrimp or mackerel to precision flow weight graders for poultry fillets, whole fish or cuttlefish, modern grading systems help producers meet both operational goals and consumer expectations.
Reach out to our specialists at info@peruza.com, we will help you choose a right grading equipment. With accurate and improved grading, processors can enhance product quality, streamline operations and build stronger trust with customers — one perfectly sized product at a time.