The dairy industry has long been a cornerstone of food production, providing essential products such as milk, cheese, and yogurt to global markets. However, traditional dairy processing methods often struggle with inefficiencies, traceability issues, and compliance challenges. With the rise of digitalization, Manufacturing Execution Systems (MES) are transforming dairy production, enabling better control, automation, and data-driven decision-making. This blog explores how MES integrates with dairy processing, improving efficiency and compliance while providing real-world examples of its impact on dairy plants.
The Shift from Traditional to Digital Dairy Processing
For decades, dairy processing has relied on manual monitoring, paper-based record-keeping, and isolated automation systems. These methods, while functional, often lead to inefficiencies, human errors, and compliance challenges. The growing demand for higher-quality dairy products, coupled with strict food safety regulations, has made digital transformation a necessity.
Modern MES solutions bridge the gap between enterprise resource planning (ERP) systems and plant-floor operations, providing real-time visibility into production processes. By implementing MES, dairy plants can track raw materials, monitor processing conditions, and ensure consistent product quality, all while minimizing waste and improving operational efficiency.
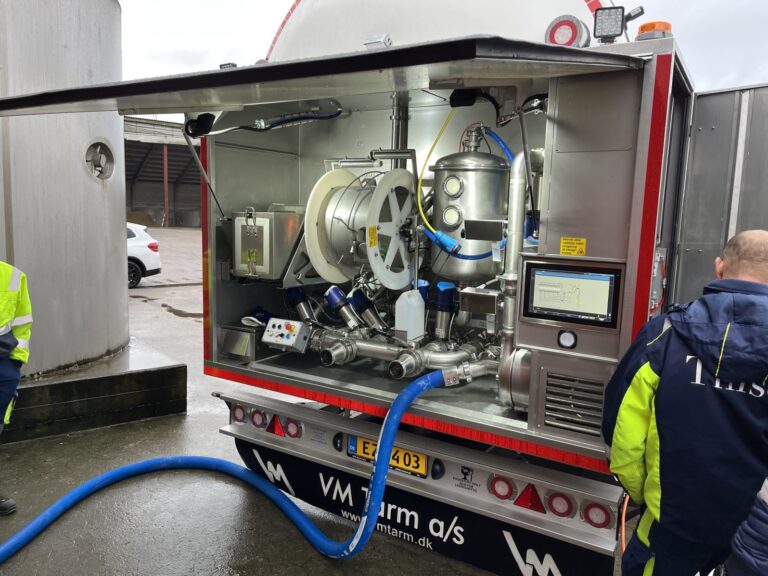
How MES Integrates with Equipment to Improve Efficiency
One of the most significant advantages of MES is its ability to seamlessly integrate with production equipment. Dairy processing involves multiple stages, including milk reception, pasteurization, fermentation, and packaging. An MES system collects real-time data from these processes, providing operators with insights to optimize performance.
Key integrations include:
- Automated Milk Reception. MES ensures accurate tracking of milk volumes, quality parameters, and supplier details, reducing errors in inventory management.
- Process Monitoring. Sensors and IoT devices connected to MES provide real-time data on temperature, pressure, and humidity, ensuring optimal processing conditions.
- Packaging and Labeling. MES ensures accurate labeling, weight control, and compliance with traceability regulations, reducing human intervention and errors.
By integrating MES with smart manufacturing technologies, dairy plants can achieve increased efficiency, reduced downtime, and improved compliance with industry standards.
Boosting Traceability and Compliance in Dairy Production
Food safety and traceability have become top priorities in the dairy industry. Regulations such as the FDA’s Food Safety Modernization Act (FSMA) and EU food safety laws require producers to maintain detailed records of ingredient sources, processing conditions, and distribution channels. Traditional record-keeping methods make compliance cumbersome and prone to errors.
MES addresses these challenges by providing end-to-end traceability, allowing dairy producers to:
- Track Ingredients. Monitor milk batches from farm to final product, ensuring product authenticity and quality.
- Automate Compliance Documentation. Generate real-time reports for audits, reducing administrative workload.
- Improve Recall Management. In the event of a contamination issue, MES enables rapid identification and removal of affected batches, minimizing losses and protecting consumers.
Case Study- Dairy's Processing Company’s Digital Transformation with MES
About the Company
To maintain confidentiality, we won’t mention the name, but it is a case study of well-established Danish dairy cooperative, founded over 100 years ago, specializes in producing high-quality cheese and dairy products. Faced with rising market demand and strict food safety regulations, the company aimed to modernize its production processes and enhance traceability to stay ahead in the industry with ScanPlant NG MES system.
Objectives of the Project
The key goals of MES implementation included:
- Improving real-time operational visibility and data-driven decision-making.
- Enhancing traceability and compliance with European food safety regulations.
- Automating processes to minimize manual errors and reduce product giveaway.
- Integrating a digital weighing and labeling system to optimize packaging accuracy.
Technical Solution
To achieve these objectives, was integrated an MES platform capable of:
- Real-Time Process Monitoring. Tracking milk reception, pasteurization, and cheese maturation parameters.
- Inventory management. Making sure to have all the ingredients and stock in place.
- Automated Packing and Labeling. Ensuring precision in packaging weight and compliance with food labeling laws.
- Advanced Data Analytics. Providing insights into process efficiency, ingredient usage, and quality control.
Results and Impact
Following the ScanPlant NG MES implementation, the company experienced significant improvements:
- Up to 2 % reduction in Product Giveaway. Optimized ingredients use and minimized production waste.
- Enhanced Traceability. Full product lifecycle tracking ensured better quality control and faster recall response. Reduced traceability audits down to 30 minutes.
- Increased Production Efficiency. Improved production yields by up to 1 %.
This transformation enabled company to scale its operations efficiently while maintaining its commitment to high-quality dairy products and sustainability.
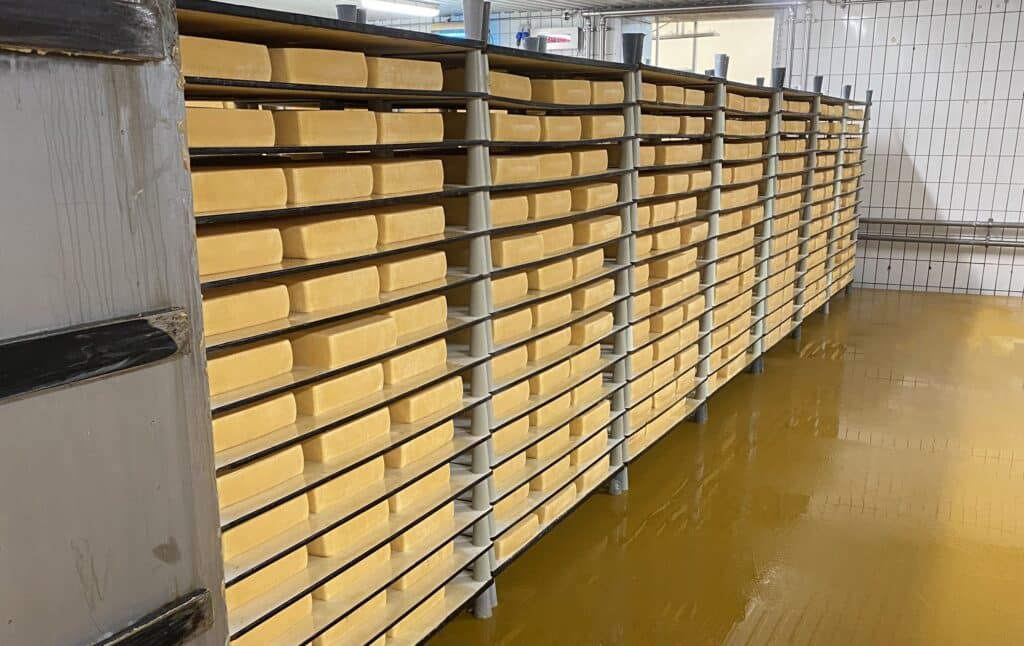
Conclusion
The digital transformation of dairy processing is no longer a future trend—it is a necessity for modern production facilities. By implementing MES, dairy manufacturers can optimize efficiency, enhance traceability, and ensure regulatory compliance. As technology continues to evolve, the integration of MES with IoT, AI, and data analytics will further revolutionize the industry, paving the way for smarter, more sustainable dairy production.
Ready to Unlock Your Potential?
As we’ve seen, reducing giveaways isn’t just about cutting costs—it’s about optimizing operations and maximizing profitability. With the right tools and strategies, businesses can achieve significant savings while maintaining product quality and customer satisfaction.
Want to learn better how to minimize giveaways and streamline your production? Join our free online webinar:
📌 Topic: Digitalization in Manufacturing- How to Optimize Production and Reduce Product Giveaways
📅 Date: February 28
⏰ Time: 10:00 (EET)
In this webinar, we’ll dive deeper into real case studies and practical methods to improve processes and reduce giveaways in manufacturing, with a special focus on dairy product processing.
👉 Register here: Webinar Link