The aquaculture industry is exponentially growing every year. Reports state that since the late 1980s, the growing trend in the total world capture fishery market has been relatively stable, with harvests ranging between 86 million and 93 million tonnes per year.
The world’s total capture fish production reached 96.4 million tonnes in 2018, the highest amount ever recorded, up 5.4 percent from the previous three years’ average. With approximately the same amounts of catch, further processing products, such as fish fingers, burgers, snacks, etc., are being produced as well.
Also, the latest industry’s tendencies show that every year more and more small-size fish are being used for human consumption. In the past decades, all of them were used just for the preparation of fish meals or other sub-products. However, processing smaller fish requires the use of suitable equipment, as typical machines can only work with larger fish.
Why it's time to turn to automated solutions?
Keeping in mind the industry tendency’s data, it’s only clear that the companies that work in the seafood industry need to find modern and up-to-date solutions for fish production to keep up not only with the high competition in the market but with meeting the industry demand as well.
Many seafood and fish-product manufacturers still tend to do the product processing manually, employing human labor, or use old-dated machines that more often than not cause more expenses, a lot of small errors, and other problems discussed further in this article.
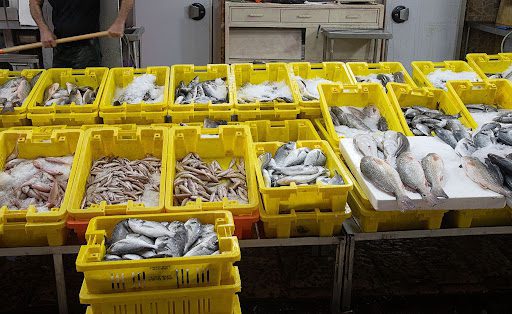
Fish-product manufacturing manually by hands
There still are many factories that use human labor in their fish and seafood processing. The reasoning behind this is that many plant managers think this is a cheaper solution than the purchase and maintenance of automated equipment.
Especially freshwater fish are more often processed manually by human laborers that are using a wide variety of knives, according to the information provided by the Food and Agriculture Organization of the United Nations (FAO).
It is said, that the manual fish process mainly is done in smaller factories. One of the main problems in manual processing is that the workers must be highly skilled to process the fish manually by hand in accordance with all the safety rules.
One of the most expensive solutions in the industry
Although many factory owners use human laborers thinking that it is a way more sustainable solution moneywise, many times it can be far from the truth. Think about how many workers you would need to hire to keep up with the seafood market demands in terms of fish production.
It is expected that the global market for seafood and fish products by the year 2027 will reach a revised size of 138.7 billion USD. Therefore the production volumes should significantly increase, reducing the production time at the same time. On average, one human laborer can properly process only a couple of dozen fish per minute, as opposed to machines that can process up to several hundred fish at that same time.
As stated before, in order to keep up with the industry standards, many human laborers need to be employed. Employment costs a lot of money because companies need to not only pay the workers their salaries but also instruct them on doing the job properly (and this training also costs).
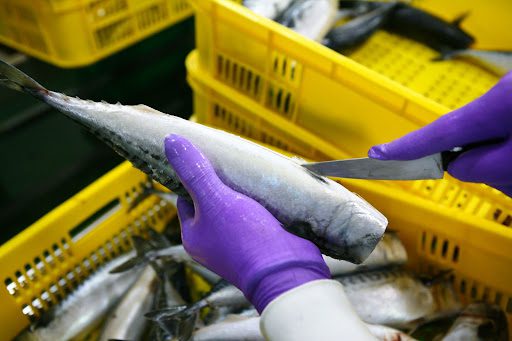
Using old-dated machines
Automated fish processing equipment, such as nobbing machines, have been used in larger factories since around the 1980s. There are some companies that are still using these types of machines in their production. But there are many disadvantages that come with using such primitive machines. Let’s have a look at some of them!
Causing a lot of fish-product waste
The old-type, simplistic nobbing machines work very mechanically – they have fixed-size pockets, where the fish are put in. The biggest disadvantage is that the machine does not adjust the cutting area according to the size of the fish, so that’s where the inaccurate cuts occur, creating a lot of wasted product.
Considering the different sizes of the fish, before the cutting process, sorting is also needed. For these old machines sorting is usually done manually, but that also creates a lot of inaccuracy – human laborers can, by mistake, put larger and smaller fish in the same bin, therefore the machine creates crooked cuts.
Easily breakable
In older fish processing machines, the pockets are made out of low-cost materials, like plastic. Compared to more complex equipment, these installations are somewhat cheaper, so, in the beginning, it might seem that this solution is much more available money-wise.
Though, materials like plastic are non-durable, causing these pockets and other elements in the machine to be fragile and easy to break. That means that these elements have to be changed every once in a while, creating additional recurring costs.
They are very hard to clean
For mechanical extraction of the fish guts, modern types of nobbing machines use rotating brushes in contrary to old-dated solutions. Older machines are using special gears that are made out of metal. These metal gear wheels tend to wrap the fish gills around themselves, making them difficult to clean.
As a result, the uncleaned fish intestines begin to rot, creating not only an unpleasant odor that factory workers have to endure but also some very serious health hazards for the fish-product consumers.
The solution – modern and upgraded fish nobbing machines
Keeping in mind all the disadvantages discussed above, it’s only clear that there needs to be a solution that evolves with time. Here, at PERUZA, our main goal is to help factories make their work more efficient, improving food processing quality, saving money, and increasing production volumes in a shorter period of time.
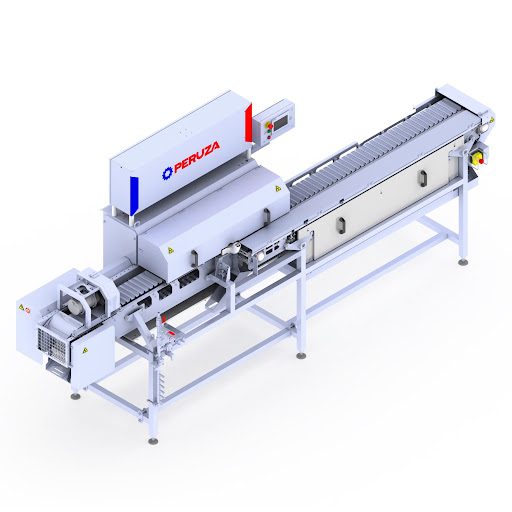
That’s why for fish-product factories we suggest our “Pocket type fish nobbing machine” that works using modern and advanced technologies. What are some of the advantages that our machine has, compared to the older solutions?
More accurate fish processing, reducing product waste
As discussed earlier, older-type fish processing machines have fixed-size pockets for all fish, making the cuts to be inaccurate. PERUZAs “Pocket type fish nobbing machine” uses smart laser-measuring techniques (or electric signals), measuring each fish separately in order to make digital and more precise measurements for cutting.
Contrary to other machines, PERUZAs nobbing machine also uses specially made plastic triangles for fixing fish heads into place, enabling a precise cutting process for both larger and smaller fish in one go (but different pockets).
Less water is needed in contrary to other machines
For putting smaller fish into its place in the pocket, our machine uses a wet rotating brush, instead of a “metal tongue” or water stream like other machines do.
Just imagine the amounts of water other machines need to make those high-pressure streams all the time! We have found a solution that can do the job without such water waste. By just wetting the soft-bristled brush, the fish gets fixed into the right position, without damaging it.
Higher production volumes in a shorter period of time
Our nobbing machine has an extensive module system, making it possible to upgrade it with other modules, for example, automatic fish orientation and feeding unit, the filleting module, or automatic packing unit for vertical cans. With using just two operators, this machine can process up to 250 fish per minute.
Complies with higher work safety standards
Other fish processing machines, especially the older ones, tend to make a lot of noise, damaging factory workers’ hearing in the long run. Working with these types of machines, special equipment, like noise-canceling headphones, is needed.
PERUZAs fish nobbing machine has a special plastic chain that allows complying with higher work safety standards and reduces system wear and noise. Compared to the other machines in the market that use metal guides, making a lot of noise, our machines are much quieter.
Final thoughts
So, to keep up with all the industry standards and high product demands in the seafood market, it is only clear that factories that want to be able to compete with others need to “step up their game” in terms of the equipment they use.
While older types of fish processing machines can do the work, they are not powerful enough to help the company stay ahead of the competitors. With over 30 years of experience in finding ways to make the production processes more efficient, we suggest that companies think about the long-term return on investment in good production techniques.